The trend
towards industrial PC's has received a permanent boost from
the development of slot PC/ PLC boards. The host CPU takes over the visualization function, while the slot PC performs the control tasks
within a system.
In the past, the industrial PC has often been used for visualization together with a conventional PLC control. The connection between the PLC
and visualization system is usually effected via a serial or a network interface. This always leads to a bottle-neck, especially as
communication has usually been performed via a DDE connection.
Slot PLC boards such as the "SPC" by TRS Fieldbus Systems are becoming increasingly popular. The core of the board is a self-contained PC. This
sub-PC is decoupled from the ISA bus by a dual-ported RAM. The sub-PC is then turned into a slot PLC by the firmware of the PLC interpreter.
The structure of the process image in the dual-ported RAM is independent of the field bus. So is the programming, which is effected on an
external laptop via an RS-232 interface. Only the data module containing the I/O definition of the field bus depends on the field bus.
The slot PLC is programmed via an AS-511 protocol, thus allowing various common programming interfaces to be used. There is a clear separation
between the visualization system and the PLC. The data transfer between both program parts is effected via the dual-ported RAM, which is
logically much faster than the conventional serial connection.
The visualization system is programmed by Visual Basic or Delphi, for example, or via any other visualization package available on the market.
For communication with the dual-ported RAM of the slot PLC, the programmer can use DLL functions and DDE servers.
This makes the system much easier than the soft PLC. The screen of the host PC is used for visualization and the screen of the laptop as the
PLC programming interface.
The advantage of the "PLC" by TRS Fieldbus Systems becomes even more apparent. When using further slot PLC boards on the same passive ISA
bus. Communication between the slot PLC boards is ensured either by mailboxes within each dual-ported RAM, whose data transfer is effected
by the host CPU, or by an additional CAN bus link between all the slot PLC boards involved.
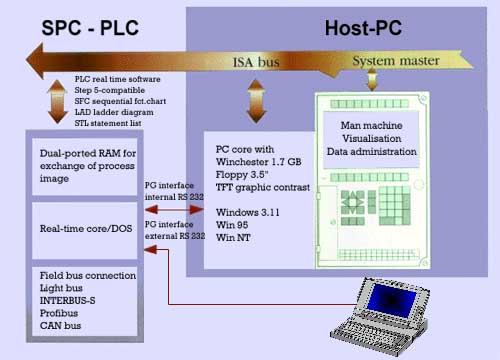
-
SPC assembly serving as
a PLC, for integration in any PC
With field bus
interfaces, e.g. for
- DeviceNet |
SPC-520 |
- Lightbus |
SPC-200 |
- Profibus-DP |
SPC-300 |
- INTERBUS-S |
SPC-400 |
- CAN bus |
SPC-5XX |
-
The "SPC" CPU
can be extended by a PC-104-VGA board, hard disk, floppy drive and
external keyboard, thus providing you with a "PC within a
PC"
-
PC kernel with 586/133
MHz and Pentium 200
-
The PLC is programmed
via the serial port COM 1 of the "SPC". This means
that the PLC can be programmed not only with the Host PC, but also via
an external laptop or a Siemens® PU. As a protocol, AS511
(or alternatively an IBH Softec protocol is used at the serial port.
-
The PLC has the
performance range of a SIEMENS 945 CPU® with respect to
operations set and speed.
-
The PLC communicates
with the higher-level host PC via a dual-ported RAM that provides the
process image.
-
Programming in S5 /
S7® (STL, SFC, LAD, graphic sequences) or in IEC1131-3
-
CAN bus link for "SPC"
- "SPC" communication.
-
DDL and DDE interfaces
with the host CPU (e.g. visualization)
-
Besides a lightbus
connection, there are further functions integrated on the motherboard:
-
interface with UPS
power supply unit (data remanence)
-
parallel interface
for special keys and LEDs
-
status display
(7-segment display)
-
switch for
start/stop, normal/special operation
-
external power
supply (12 V... 24 V DC)
-
128 Kbyte buffered
SRAM
-
4 Mbyte (10 Mbyte)
flash
®registered trademark
of Siemens AG
visualization of the PLC
program is usually effected with an external laptop or programming unit
via a serial port. By this means, online interventions in the normal way
are possible. While the PLC is viewed as it were from the outside via the
serial port, the host CPU views the PLC from the inside via the dualported
RAM. An action in the host PC, e.g. pressing a key of the visualization
interface, triggers a reaction in the PLC which can then be observed
simultaneously on the programming unit. The dual-ported RAM interface
between host PC (visualization) and SPC (PLC) connects both program parts
without either part directly influencing the other. Screen masks,
higher-level routines etc. have no effect on the cycle time of the PLC, as
these run completely autonomously on self-contained hardware.
In each cycle, the slot PLC
refreshes the process image within the dual-ported RAM that constitutes
the interface between PLC and host PC, so that the user is supplies with
all the data of the PLC. For visualization of the process image of the SPC
(slot PLC), all modern tools can be used. DLLs (Dynamic Link Library) as
well as various DDE interfaces (Dynamic Data Exchange) are available from
TRS, for example. Adaptions to various commercially available
visualization packages have been and are being created. We are open to any
requests of the nature.
If several slot PLC boards
are combined on a common ISA backplane, the host PC can of course write
and read data from all PLC boards, i.e. visualize several PLCs
simultaneously. Available programming interfaces are S5 for Windows and
IEC1131. The picture above shows some extracts from the PLC programming
interface.
|